5 Mar
从原矿到电池制造——锂离子电池原材料污染分析
摘要
锂离子电池生产所用材料中的杂质和污染物会对成品产生灾难性的影响。因此,必须在整个生产过程中对材料的质量和清洁度进行监测,发现污染物并控制其来源。质量监测必须贯穿整个生产过程,从矿山生产的原材料到最终的电池级粉末。
本文介绍了一种利用扫描电子显微镜(SEM)和能谱仪(EDS)对电池原料粉末中的杂质进行自动检测和识别的方法。通过在生产过程的不同步骤取样,可以确定污染物在哪个步骤被引入,从而判断污染源并制定后续的解决方案。
引言
锂离子电池在过去十年中一直是一项关键技术,也是电动汽车行业发展的一个重要组成部分。锂离子电池生产所用材料的纯度必须非常高,以避免金属颗粒击穿绝缘隔膜而出现严重事故,并保证电池具有理想的性能和寿命。
质量控制在整个制造过程中都至关重要,因为即使是极少量的污染物也可能导致灾难性后果。
电池中使用的金属,首先从原矿中提取出来,此时需要检验提纯金属的纯度,随后,材料通常被运输到材料加工厂加工成为前驱体,最后供应给电池制造厂。在整个过程中有多个潜在的污染源,这意味着必须在每个阶段都要监控材料是否被污染
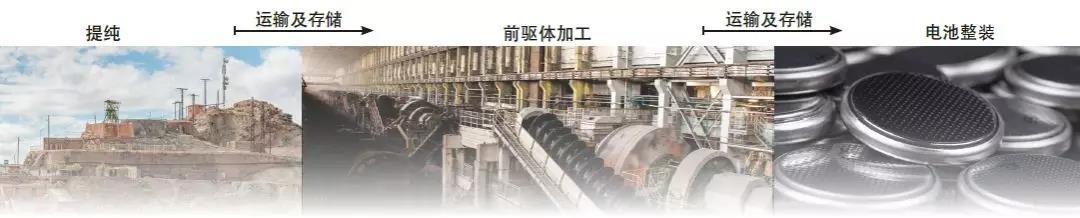
锂离子电池的每个生产阶段都涉及到基于能谱仪的显微成分分析:
● 自动化矿物相分析
● 污染物鉴别
● 质量(纯度)鉴定
● 原材料(Ni/Co/Mn氧化物)清洁度分析
● 监控生产流程以确保没有引入污染物
● 成品表征(成分、清洁度和颗粒尺寸)
● 前驱体清洁度分析
● 研发(Li检测,元素分布,相构成等)
失效分析(电极上的裂纹和第二相,充电/放电循环引起的微观结构变化)
用于组装电池的前驱体,必须保证其中没有杂质,去除杂质是一个既耗时又昂贵的过程。因此,需要有一个简单、可靠、快速的方法来识别杂质,以保证产品合格。
目前市面上最常见的锂离子电池,阴极都是由镍、钴和锰的化合物所制成。作为其中不可或缺的元素,对Co原矿石的开采量及质量要求越来越高,其价格也居高不下。因此,保证材料不受污染是成本控制中尤为重要的环节。
本文中,我们考察了CoO粉末中的银、铜或锌的大颗粒(直径大于1μm)的污染物分布情况,这些污染物最可能导致终端产品失效。
实验内容
利用背散射电子(BSE)成像探测器结合EDS分析,可以在SEM中鉴别杂质颗粒。平均原子序数较高的颗粒在BSE图像中显得更亮,选中这些颗粒后,并进行EDS采集。在分析大量颗粒时,手动选择并检测耗时耗力,并且可能存在误差(如,漏看视场内的颗粒,观察区域不够大等)。AZtecFeature提供了一种自动的检测分析方法,在保持高空间分辨率的同时,能够快速定位、识别分布整个样品区域上的所有颗粒并对他们进行分类统计。
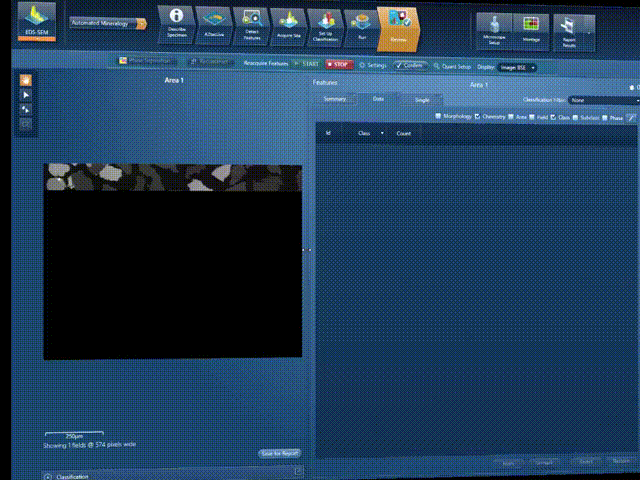
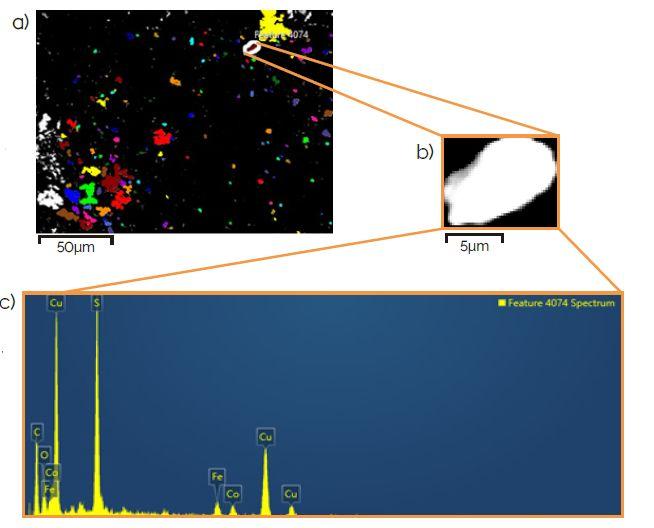
图2的例子使用了AZtecFeature对样品进行自动颗粒物检测。首先,根据BSE图像中颗粒的灰度设置相应的灰度阈值,识别颗粒,确定位置并测量形态参数;随后,对检测到的颗粒进行成分采集,根据成分信息利用分类方法可以对这些杂质颗粒做自动分类统计。
讨论
本文使用AZtecFeature分析了三个样品,分别来自矿场、运输卡车和加工厂。矿场样品和加工厂样品直接由碳导电胶带蘸取,而卡车样品则是从滤尘器中收集的,3个样品均采用牛津仪器Ultim Max170及AZtecFeature系统进行分析。
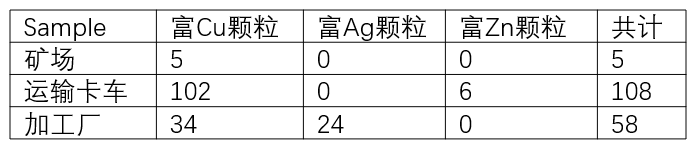
该矿的原料不含锌、银,只有少量铜。运货卡车上的灰尘样品中含有大量富铜颗粒,这也解释了加工厂采集的样品中铜颗粒较原料多的原因。银杂质应该是在运输后期引入的,可能与加工厂环境有关。
有多种方法可以用来去除材料中的杂质颗粒,但都耗时且成本较高。通过确定污染颗粒是在哪个流程中引入,可以节省大量的时间和金钱成本,从源头上解决问题。在这个案例中,对运输阶段实施简单的清洁控制可显著减少Cu污染。此外,数据表明,加工厂也发生了污染,可以进一步调查在这一阶段杂质颗粒来源,这很可能是来自其他工艺管线或材料处理的污染,之后据此进行工艺环境清洁控制或流程优化等。
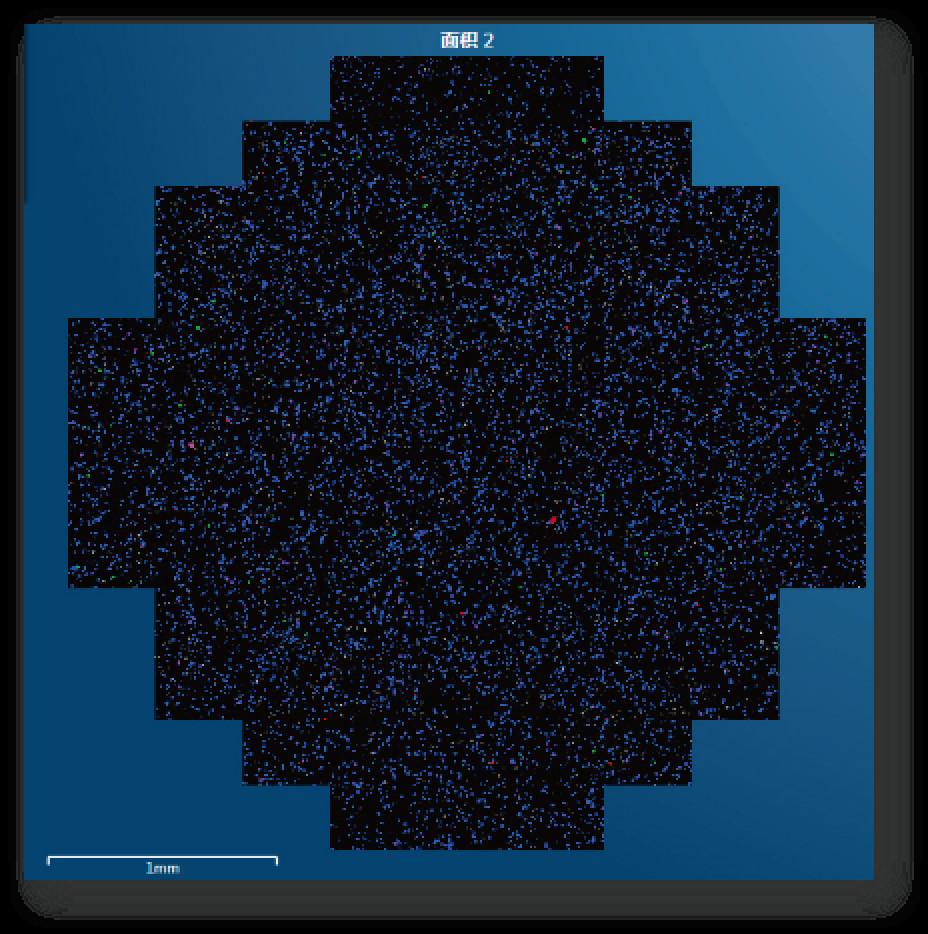
结论
AZtecFeature提供了一个简单快速的污染物识别、统计的解决方案,可以监控从矿山到最终产品所有步骤的材料质量,这对于电池行业的质控和成本控制都至关重要:如未能明确污染物来源而需在最后阶段提纯样品,成本昂贵;而如果未能监控杂质颗粒,这极有可能会对最终的电池产品造成严重的后果。
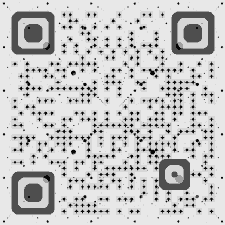